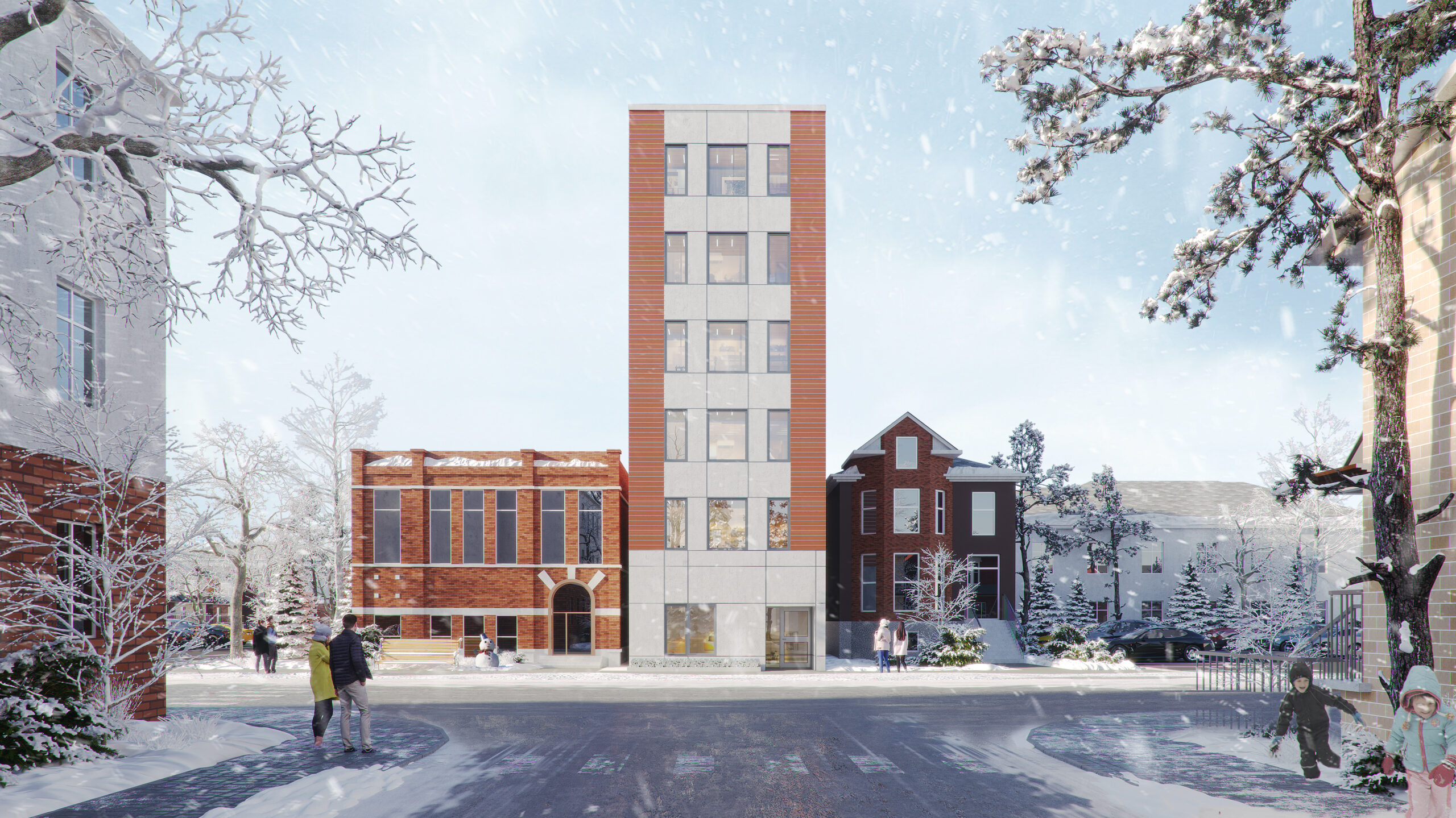
St. Matthew’s House
412 Barton
Opportunity
The 412 Barton project was initiated in response to the client’s need to develop transitional affordable housing in Hamilton, addressing the pressing demand for supportive housing within a highly constrained urban site. The client sought a design solution that maximized available space while ensuring the delivery of a cost-effective, sustainable, and rapidly deployable housing model. The project posed unique challenges, including a narrow 6.5-meter-wide footprint and a zero-lot line condition, requiring a strategic approach to space planning and construction. The client also aimed to incorporate mass timber construction to achieve sustainability goals and expedite the building process, necessitating an innovative design approach that balanced regulatory compliance with functionality and efficiency.
Response
Initial designs focused primarily on site and envelope considerations, which necessitated a comprehensive reconfiguration to incorporate essential mechanical and support spaces. Given the absence of a basement or lower level, all mechanical services were strategically integrated into the first floor, requiring meticulous planning within the tight spatial constraints.
A key innovation in the project was the use of Nail Laminated Timber (NLT) instead of the more commonly used Cross Laminated Timber (CLT), which offered benefits in speed and suitability for the project while posing additional permitting challenges with local authorities. Structurally, the building’s slender proportions required the implementation of a robust steel brace frame at the rear to ensure stability while maintaining the project’s spatial and programmatic requirements.
The prefabricated modular nature of the project introduced a phased documentation approach, where detailed drawings were incrementally provided to meet rapid housing deadlines. Special attention was given to the coordination with panel fabricators to ensure architectural intent while avoiding redundant detailing. Site constraints further necessitated a construction approach that relied on building from the inside out, requiring precise sequencing and close collaboration with the construction team.
Project Facts
-
Markets
-
Services
-
Location
Hamilton, Ontario
-
Size
9,996 sq. ft.